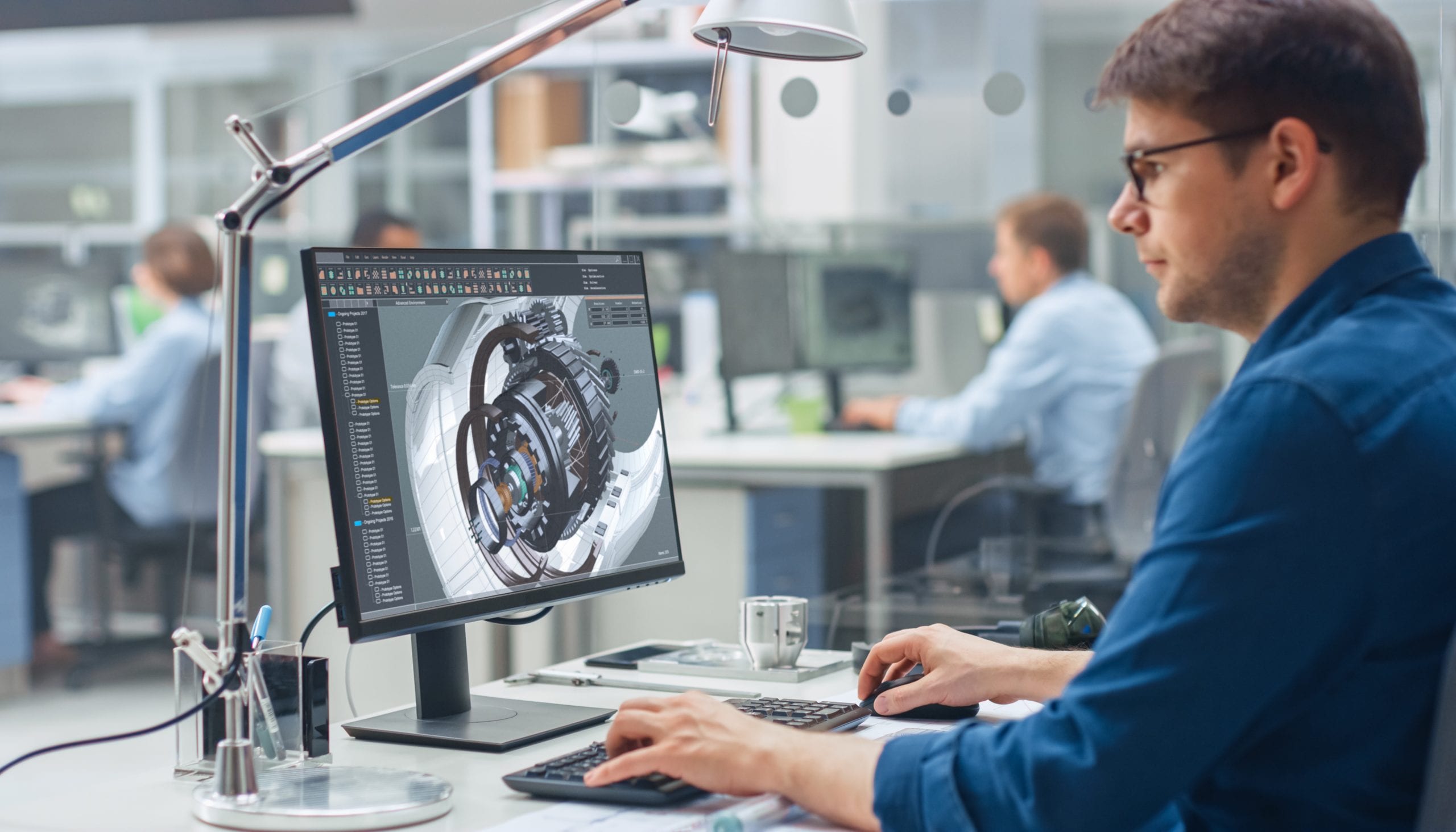
5 Industrial Design Best Practices for Good Quality Products
January 22, 2020
Have you ever received a shipment of product with an error that renders the whole order a loss? How many hours or days did you waste trying to find the source of the problem and negotiate a replacement? More importantly, what was the cost of this error to your bottomline?
Outsource manufacturing means putting trust in your vendors. Hoping your products arrive exactly as you need them is often exactly that: hoping. Having a good quality management system (QMS) not only affects your company’s output, but also how willing your customers are to trust your brand and buy your products.
Often, problems occur due to a miscommunication of design requirements that could be avoided by implementing some simple rules of thumb.
Here are 5 industrial design tips to help you eliminate finger crossing and take control over the quality of your order from the very beginning.
- Stay Consistent and Standardized
Choosing a consistent unit of measurement to use throughout your designs is essential. Unnecessary opportunities for miscalculation and costs arises when a factory has to convert your measurements or tooling into its native unit.
Use universal standard units of measurement wherever possible. The metric system is used by most global manufacturers. Utilizing ISO, ANSI, or MIL-SPEC standard processes and measurements can eliminate opportunities for ambiguous interpretations. Stay consistent and standard wherever possible.
- Spec Everything
When we say specify everything, we mean it. Any unspecified elements of your designs are left to the imagination of your factories. Each and every surface, edge, tolerance, material and treatment must be clearly labeled.
Pay special attention to coatings and edges. If you do not specify a coating, the factory will choose a standard coat. What you expect to be bare metal components may arrive with an unwelcome powder coat. Any edges that have not been labeled for deburring could arrive sharp enough to puncture an inspection glove. Leave no stone unturned.
- Check for Tolerance Stacks
Tolerance stacks are a complex study of their own. However, you can ensure the quality of a component by keeping the end product in mind. When building an assembly, every component has to fit together and have clear +/- specifications. Make sure every component is prototyped, fitted and tested against the final product assembly before you place an order.
- Keep it Simple
Keep your material process in mind in the design phase. Whether its a multi-component assembly or standalone part you will save time, money and margin of error by keeping your designs as simple as possible.
Think from a machining perspective: how many moves or steps are required to make your product?
For example, in a machined metal component rounded corners require a single drill or sweep to cut or form, where hard corners require the machines to shift and pivot to create an angled cut or corner. For machined products, if an angled corner is not essential to the function or aesthetic of your product, you may want to consider making it round to reduce the risk of errors.
- Change the Way you Think About Quality Management
Quality management and QMS’s are traditionally viewed as end-of-run procedures and processes. Checking for the quality of a product after it has been made is essential, but viewing quality management as an end-to-end process creates greater product success. It is time to implement best quality practices throughout every stage of manufacturing, starting from the designs. Achieving transparency, clarity, understanding and trust throughout your communications and relationships with your vendors will create better products and a better future for your supply chain and outsourced manufacturing.
Quality from Beginning to End
There are several simple steps you can take in the design process to set your products up for success. End-to-end quality management systems will take hoping out of quality management and give your company certainty that will save you time, money and frustrating non-conformance analyses.
Start a free trial and experience the supply web in action.
Author
Christina Lionello
Marketing and Communications Specialist at Omnae