Smart Supply Webs: The Shared Single Source of Truth
January 22, 2020
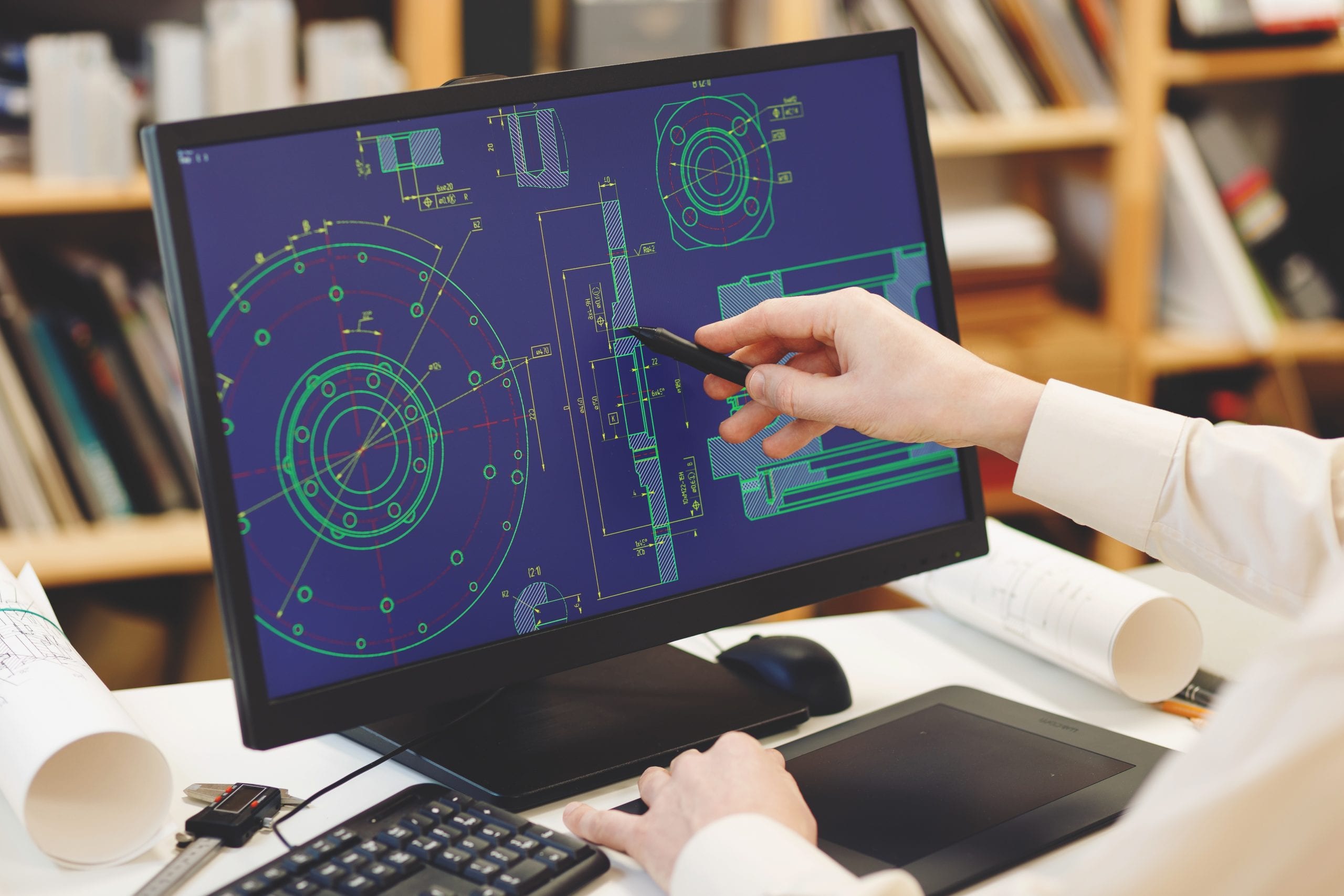
A Whole New Level of Collaboration
The need for a single source of truth (SSOT) within your company isn’t groundbreaking news, but the ability to share one record between companies is. Not only do you need a centralized and irrefutable record of all your information, data, communications and agreements, but you need the ability to share that information with your outsourced manufacturing partners.
A Shared Single Source of Truth doesn’t belong on the Nice-to-Have List – it is a requirement for the modern supply web.
Intra-Company vs. Inter-Company
Traditionally, the SSOT has been an internal, or intra-company resource. This means that your company has access to a central repository of information, which benefits company alignment and efficiency. In many organizations, this takes the form of a project management tool or public drive containing countless spreadsheets, documents and logs. Training and standard operating procedures are required to ensure that every member of your company keeps the information properly logged and up to date.
Having a collaborative or inter-company Shared SSOT means that you and your outsourced manufacturing partners both access, contribute and refer to the same set of information housed within one central system. This requires a collaborative tool with portals for both (or all) companies in which a singular set of information is synchronized and continually up-to-date. Having a Shared SSOT means your companies can stay in agreement throughout complex manufacturing projects, save time and money by eliminating repetitive data entry and opportunities for miscommunication and ultimately build valued and trusted relationships.
Always in Agreement
Maintaining a Shared SSOT creates a record of agreements between companies. Proactively establishing clear expectations is integral to successful outsourced manufacturing relationships and producing good quality products. A Shared SSOT provides a record of every agreement between companies that each must verify and comply with. With a Shared SSOT, if a deadline is missed or part is non-conformant, it is simple to refer to your collaborative agreement and deduce the root cause of a problem. Quality management is also made simpler with a Shared SSOT by creating a standardized set of data management procedures. For manufacturers, this simplifies the processes of quality control and non-conformance reporting as well as ISO certifications and audits.
Shared SSOTs ensure that you and all of your outsourced manufacturing are always in agreement on:
- Data management procedures
- Part Specifications
- Revisions
- Order Details
- Pricing
- Shipping and Delivery Dates
- Quality Control
Simple, Secure and Standardized Data
Constant data replication is not only tedious and time consuming, but exposes your information to opportunities for error. The need for repetitive data entry and reconciliation is drastically reduced with a Shared SSOT.
The data journey with an internal SSOT involves numerous replication points. As a manufacturer, your engineer will create a part and log its details in a spreadsheet. Those part details will be copied into your purchase order log, and further again copied into your invoice log and shipping log. All of the information would be identical, however manual intervention is required to move it from one log and department to another. Upon order, your vendor would receive your information and replicate the part details into a production log and shipping log; their own, separate internal single source of truth.
With a Shared Single Source of Truth, the part details would be inputted once at the creation of an RFQ or order. The same information would be automatically accessible in the parts’ record and carried forward across every stage or pre-production, production and logistics for every company involved. This practice can be applied to every detail of your parts, orders, revisions, quotes, invoices, contact information, shipping and billing. Information only has to be entered once for it to be accessible by every department in each company. Furthermore, any changes are automatically updated system-wide. Manual intervention is decreased immensely, saving time, money, and data risks.
Collaborative Certainty Builds Trust
Collaborating with your outsourced manufacturing partners to ensure you all have clarity and agreement on every aspect of every product and order gives you confidence. Having confidence in your supply web relieves stress from your team and creates trust between companies. A trusted relationship is invaluable in the world of supply web management and will save you time and money on trial-and-error sourcing, management and set-up costs.
If you can trust in your information, and trust your suppliers, then you can trust that your products will be top quality every time.
The time savings, reduction in margin of error and confidence provided by having a Shared Single Source of Truth cannot be overlooked. It isn’t a question of whether or not you need a Shared SSOT, but when you need it; and the answer is yesterday.
Start a free trial and experience the supply web in action.
Author

Christina Lionello
Marketing & Communications Specialist at Omnae